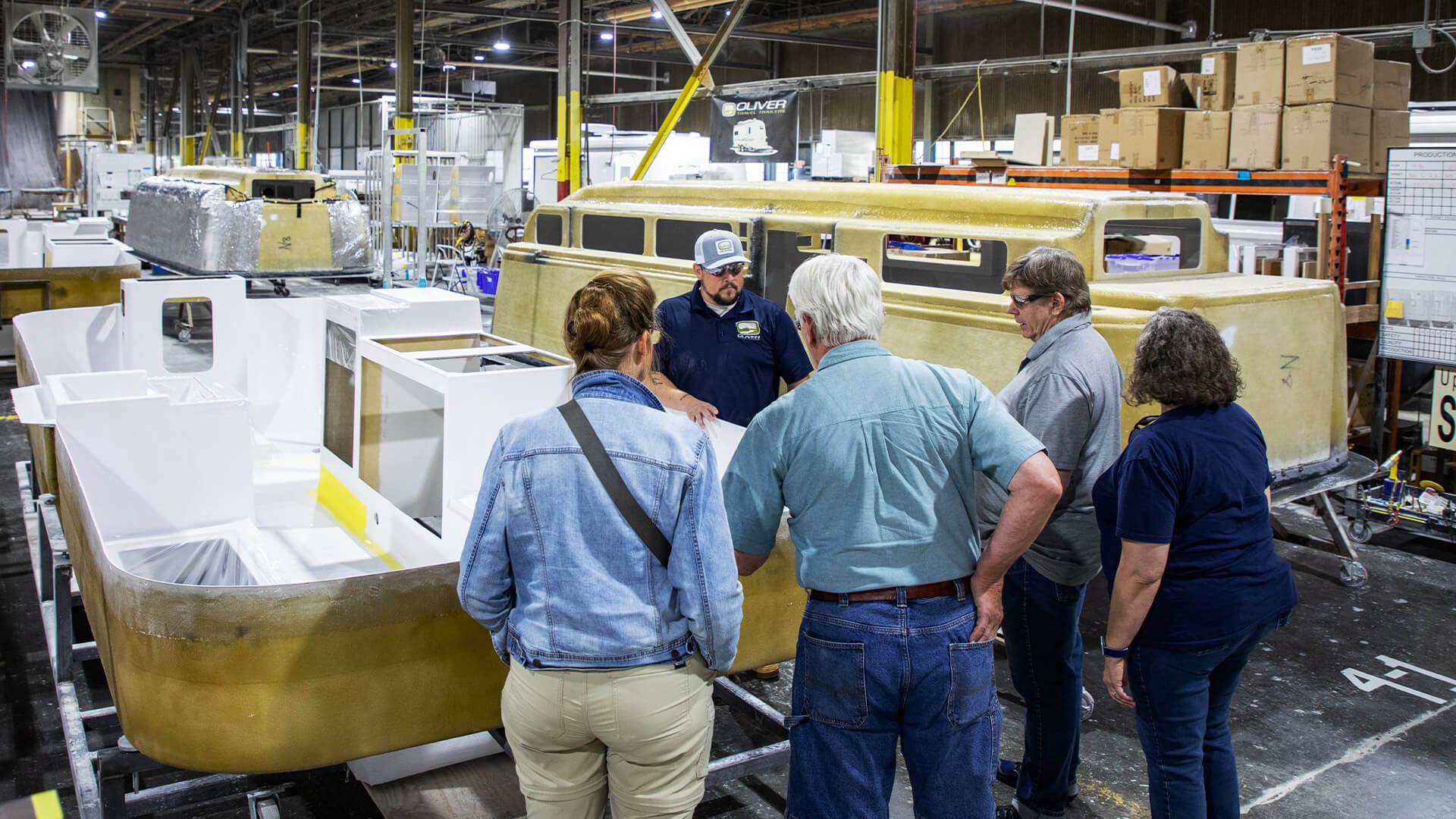
Travel Trailer Manufacturing
Discover What Sets Oliver Apart
Since 2007, Oliver Travel Trailers, based in Tennessee, has been crafting premium travel trailers renowned for their exceptional quality and durability. With innovative design and a commitment to customer satisfaction, Oliver has earned a stellar reputation, consistently celebrated by thousands of owners and industry experts alike.
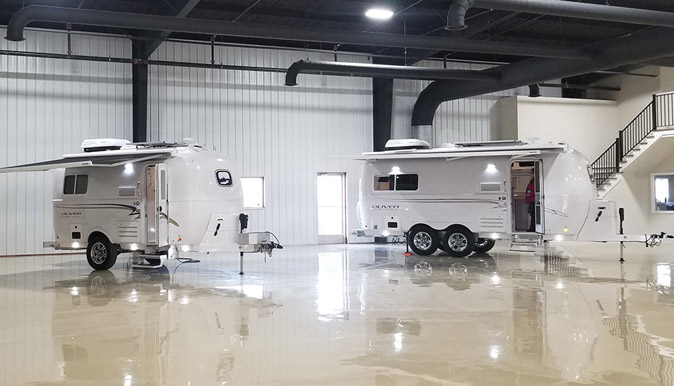
Born from Passion, Built for Adventure
Born from the Oliver family's love for camping, our trailers offer durability, beauty, and hassle-free setup and maintenance. Effortless to tow, they're ideal for all campers and often become beloved destination trailers.
Learn MoreOur Commitment to Quality and Craftsmanship
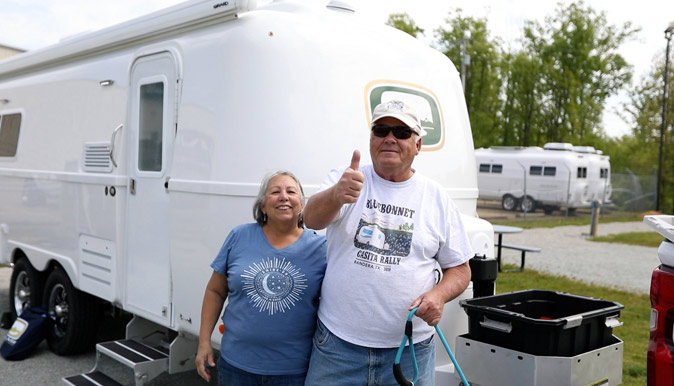
Your Satisfaction Drives Everything We Do
At Oliver, customer satisfaction drives everything we do. We deliver excellence through premium materials, expert craftsmanship, and dedicated support, ensuring every customer receives exceptional value.
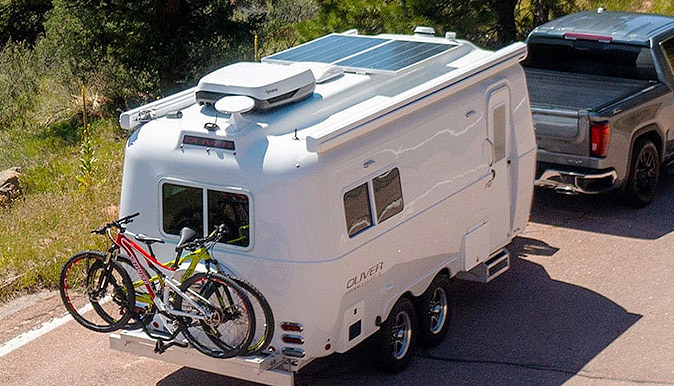
Quality, Resilience, and Record Sales
Oliver Travel Trailers launched the 18′ 5″ Legacy Elite in 2007 and the 23′ 6″ Legacy Elite II in 2008, both celebrated for their fiberglass quality. Production paused briefly in 2008 due to economic conditions but resumed in 2013, driving record-breaking sales every year since.
Learn MoreFiberglass Construction: Durable, Beautiful, and Low-Maintenance
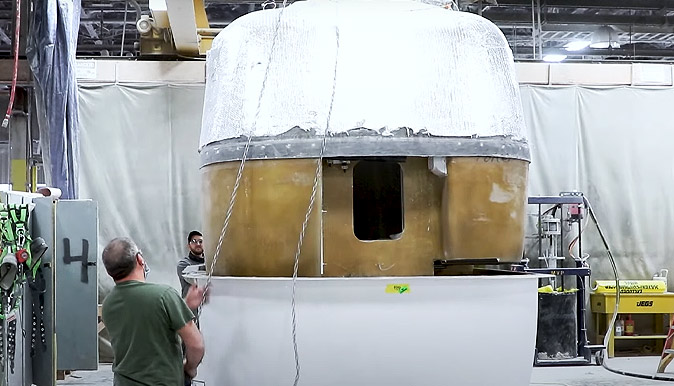
Precision Fiberglass Construction
Oliver travel trailers are crafted from four fiberglass shells—two inner and two outer. The lower outer shell is bolted to an aluminum frame and fitted with wiring, plumbing, and tanks. The two inner shells are bonded to form the interior, complete with seats and cabinets, then finished with lighting, doors, and cutouts. This interior is set into the lower shell, connected, and topped with the upper outer shell.
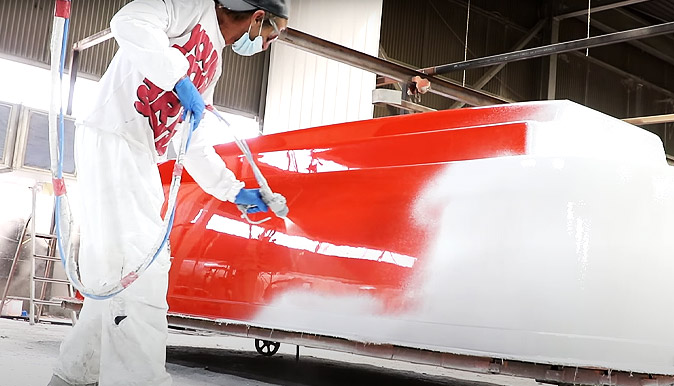
Sleek, Durable, and Built to Impress
Oliver Travel Trailers’ team strives for a flawless mold surface, blending stunning looks with lasting durability. This dedication to quality raises the bar in the industry, delivering a sleek, elegant exterior that showcases the brand’s exceptional craftsmanship.
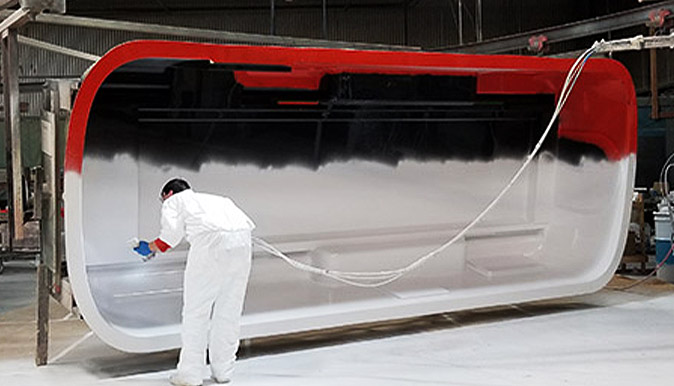
Built to Last, Designed to Shine
Our trailers feature a durable gel coat that resists chipping from road debris and fading from sun exposure, thanks to built-in UV protection. This keeps your Oliver looking sleek and stunning for years.
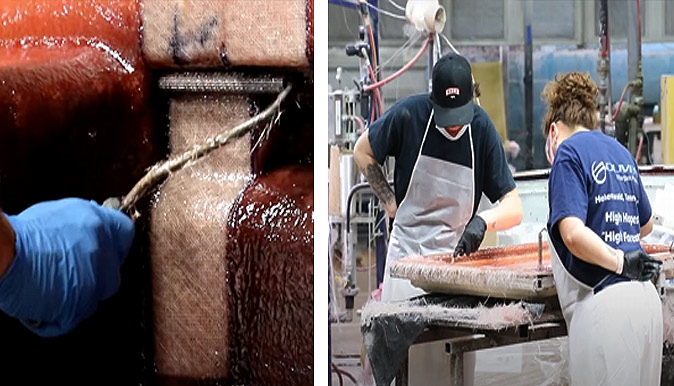
Strength in Every Layer
After applying the gel coat, we add a hand-rolled layer of resin and chopped fiberglass, eliminating air pockets for unmatched strength and durability. This meticulous approach showcases Oliver's dedication to building trailers that last.
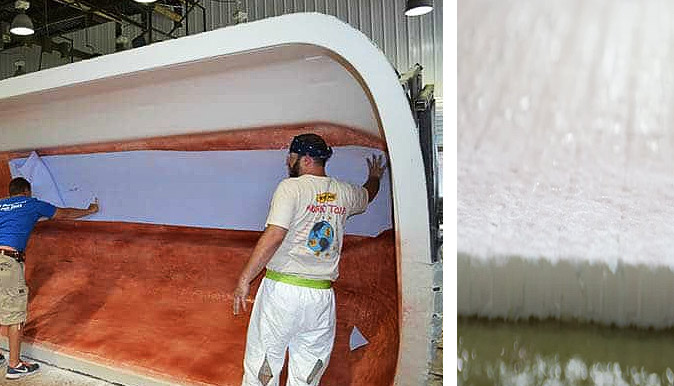
Strength Without the Weight
A core mat is glassed into the roof, reinforcing the trailer’s structure while keeping it lightweight. This boosts durability and resilience, ensuring your trailer can handle the road for years.

Built for Strength, Designed for Comfort
Oliver uses carbon core, a lightweight honeycomb composite, to strengthen roof and wall structures. This material boosts durability, insulation, and energy efficiency, ensuring your trailer stays comfortable and resilient on every adventure.
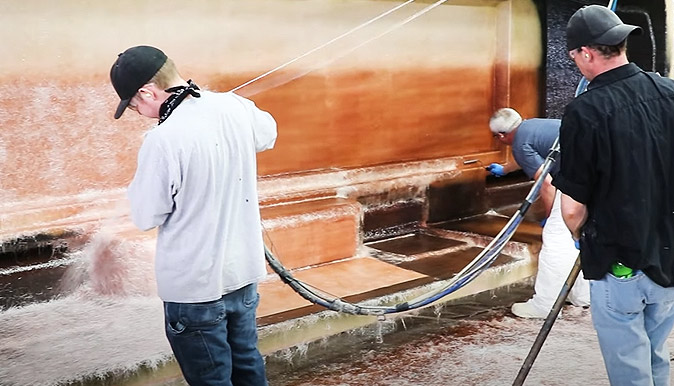
Hand-Laid Layers for Strength and Stability
We hand-lay two layers of woven mat and a bi-directional glass cloth on the outer lower shell's channels to strengthen the frame-body connection. This boosts the trailer's strength, with the mat providing tensile strength and the cloth adding multi-directional durability, ensuring stability and longevity.
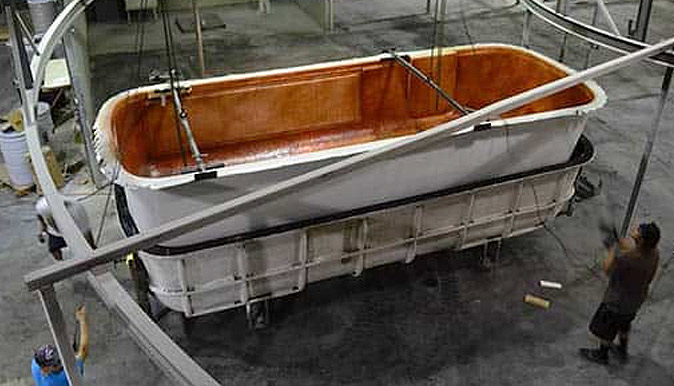
From Mold to Masterpiece
After the fiberglass shells harden, we carefully remove them from the mold to preserve their integrity. This efficient cycle—inspecting, prepping, and restarting for new shells—ensures every trailer meets our high quality standards.